Market Trends
The reporting year was a significant period for the mammalian and microbial market, with worldwide biopharmaceutical sales currently at USD 258 billion and estimated to grow at a CAGR of 9% over the next six years1. There has been strong venture capital (VC) funding for biotechs, which has supported this healthy growth in development and had a positive impact on outsourcing to custom manufacturers like Lonza.
The product landscape is changing rapidly and is getting more complex from a regulatory perspective, with an increasing need for new molecule design, manufacturing technologies and process improvement capabilities for biologics. Mammalian will remain the preferred production technology and has the highest growth potential due to pipeline increase and improvements in manufacturing technology. However, the sales of new molecular formats is predicted to grow at up to three times the rate of standard monoclonal antibodies (mAbs) through to 2025, including antibody drug conjugates (ADCs) and bi-/multi-specific antibodies, among others2. Bispecifics and other more complex molecules also require new technologies for expression systems. These will include improved cell lines and manufacturing advances, such as continuous production.
New challenges are also brought by accelerated approval pathways such as FasTrack and Priority Review, which have increased pressure to quickly deliver therapies to the patients who need them most.
In biologics, many companies recognize that development failures often relate to poor formulation and poor drug product design. All biologics for systemic administration are parenteral and are administered by injection, infusion or implant. Such modern subcutaneously administered products require a high product concentration, which requires a careful formulation development to cope with the resulting risks of high viscosity and aggregation. Other modern products, such as in immuno-oncology, require very low doses alongside careful design of the drug administration setup. This is critical to ensure that the low quantities are actually reaching the patient.
Product failure at the formulation or final-filling stage accounts for significant cost and timeline challenges. Specialized expertise in drug product development, manufacturing and testing is required to ensure fast commercialization and robust production.
A growing number of molecules in the pipeline are expected to be owned by small and virtual biotech companies, who may not have the in-house expertise to bring those to the market and therefore have a higher propensity to outsource. Biotech is outsourcing more than 70% of its services to external partners3. In smaller biotech, this number reaches between 90 and 100%, as secured funding is used for developing therapies, not manufacturing for clinical stage trials2.
VC funding is critical in this space – and biotech companies with a strong manufacturing partner receive better funding. VC funds have now begun to set up virtual biotech companies. Such virtual companies do have only a skeleton crew of managers. Therefore, high levels of communication, coordination, and trust among partners are prerequisites to deliver a successful outsourced project. Additionally, there is a burgeoning ecosystem of small pharma companies in China, supported by strong access to VC funding and bolstered by expectations of biologics growth.
1 Source: Evaluate Pharma (2019)
2 Source: Visiongain (2018)
3 Source: BioPlan Associates (2018)
Our Offerings
We are a leading contract development and manufacturing partner for biopharmaceuticals. Our offerings include a wide range of contract development and manufacturing services from sequence optimization, cell line construction, process development and optimization, and manufacture of drug substance and drug product for mAbs and other recombinant proteins from mammalian cell culture and microbial fermentation in small to large scale. Additionally, we specialize in development and manufacturing of bioconjugates which exemplifies our competency in developing and manufacturing complex molecules. We work in partnership with customers of all sizes, from start-ups to large biotechs and pharmaceutical companies.
In 2019, we offered a broad portfolio of drug substance and drug product development services, as well as clinical and commercial supply manufacturing in mammalian and microbial expression systems. Currently our development and manufacturing product portfolio includes active pharmaceutical ingredients (APIs) for life-saving medicines, including cancer treatments and orphan drugs for rare diseases where no alternative treatment exists.
For our customers in late discovery phase, our Applied Protein Services offering includes technologies and programs designed to assess and mitigate risks, reduce attrition and improve the quality and safety of therapeutic proteins in a cost-efficient and timely manner. These technologies include our Epibase® in silico and in vitro, immunogenicity screening, and our antibody humanization and deimmunization services.
Our Sentinel APARTTM Platform serves as a tool for antibody aggregation prediction and re-engineering, and our manufacturability assessment service is used to help predict and mitigate manufacturing risk. Early-stage customers also benefit from our mammalian and microbial-based LightpathTM material supply services for their research and proof-of-concept studies. We also complement these services with developability assessment services to support our customers’ lead candidate selection. More information on our late discovery services is available online.
When a lead candidate is selected, our industry-leading expression technologies, including the GS Xceed® Gene Expression System for mammalian expression and XS® Microbial Expression Technologies for microbial expression, are used to create commercially relevant cell lines or strains for protein production. Our GS Expression System® now underpins dozens of commercially available products, plus hundreds of others in clinical trials. We are continuously building on our established and trusted platform to ensure it remains a powerful solution for next generation bioprocessing, including the expression of increasingly complex proteins and continuous processing.
Following the creation of a new cell line or strain, we engage in a program of process development and scale-up studies that creates a robust process suitable for transfer to current good manufacturing practices (cGMP) sites. Once a process has been established, we can manufacture products to support not only preclinical activities, but also clinical trial material. In addition to developing a process at Lonza, we are also able to transfer into Lonza many product and process technologies that have been developed by our customers.
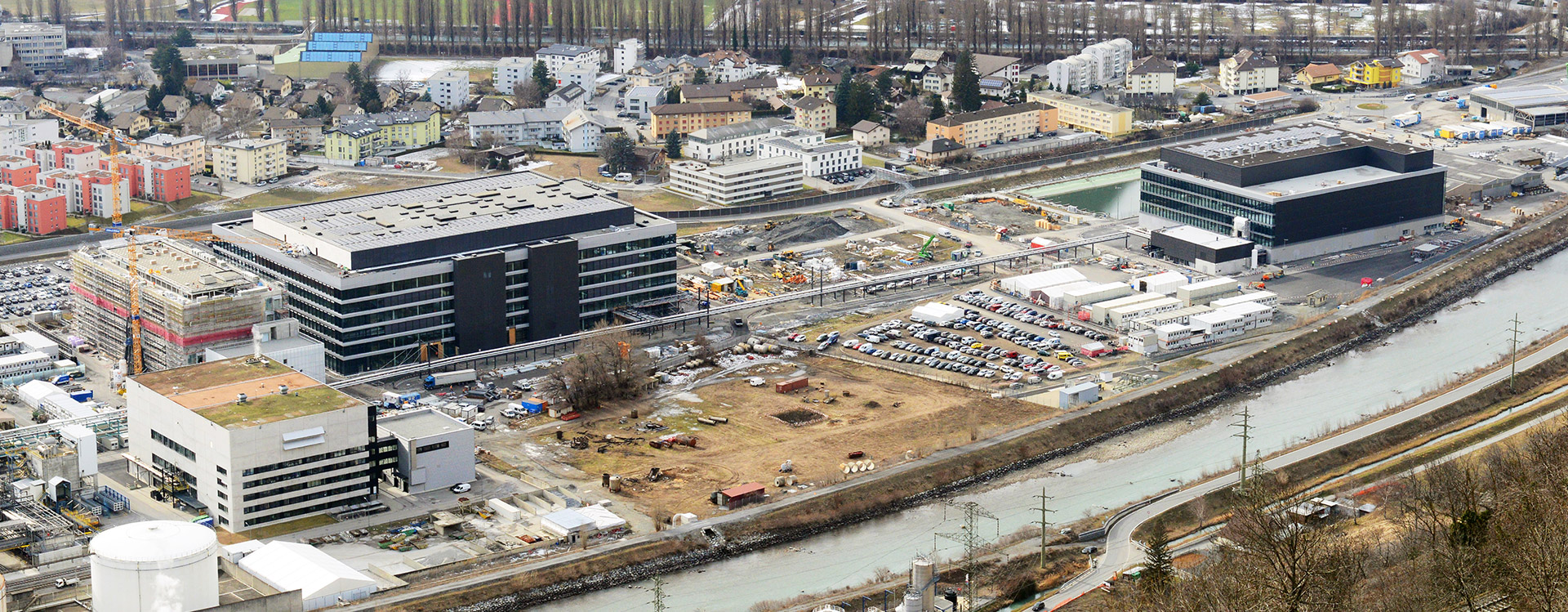
IbexTM Solutions
IbexTM Solutions consist of three innovative contract development and manufacturing organization (CDMO) offerings that span the complete product lifecycle of a biopharmaceutical – from preclinical to commercial stages, from drug substance to drug product, all in one location.
The three offerings IbexTM Design, IbexTM Develop, and IbexTM Dedicate have been developed as a response to a dynamic market and evolving needs. The home for IbexTM Solutions is the Lonza biopark in Visp (CH), which leverages Lonza’s existing infrastructure, support networks and a stable and highly skilled workforce.
IbexTM Design is our offering for customers’ preclinical and Investigational New Drug (IND) needs through to clinical Phase I. It includes a pioneering gene-to-drug product package for antibodies and antibody-like molecules, delivering drug product within 12 months and at least 1 kg of drug substance1. This package also includes the reservation of a manufacturing slot for clinical resupply. Customers can benefit from our proven GS Xceed® Gene Expression System bioprocess platform and a holistic development strategy with the endpoint in mind.
IbexTM Develop helps companies seamlessly and rapidly transition from clinical Phase II to commercialization. Co-location at one site eliminates the need for tech transfers, and accelerates the path to market. This offering enables biologics license applications (BLAs) to be submitted within 22 months from the start of process characterization. Eliminating the need for tech transfers, driving process optimizations and creating operational efficiencies are all expected to accelerate the path to market.
With IbexTM Dedicate, a fully customized commercial supply solution for our customers’ products, Lonza is able to offer complete product lifecycle management in one site. A pre-built shell and faster ramp-up could save our customers up to 30 months total time to market. IbexTM Dedicate allows our customers to delay their capacity build decisions and better manage investment risk. Moreover, our technology-agnostic supply solutions provide for flexible ownership and operating models for mammalian and microbial production, vaccines and cell and gene therapies.
* Image as of January 2020
1 From receipt of the gene sequence, subject to contractual terms and conditions
Parenteral Drug Product Services
Our Drug Product Services (DPS) team in Basel (CH) focuses on parenteral dosage forms and offers solutions for customers developing therapeutic proteins, peptides, cell and gene therapies as well as small molecules that require a parenteral dosage form. These products are for injection, infusion, intravenous, subcutaneous and intraocular routes of administration.
The DPS team provides a complete portfolio of services for parenteral dosage forms, including formulation development, simulated clinical administration setup and testing, analytical method development and quality control. Further services include primary packaging and device design and integration, drug product process development, and manufacturing of parenteral dosage forms for stability testing and preclinical or clinical testing.
There are also special services including surfactant characterization and characterization of excipient degradation, extractables and leachables assessment, and container-closure integrity and device testing. Our experts have multiple years of experience in the development, manufacturing, testing and commercialization of parenteral dosage forms and related regulatory requirements. Many of our experts have extensively researched and published in this area. Our customers benefit from seamless integration of pharmaceutical ingredients and drug substance development for rapid and reliable entry into the clinic and for robust late-stage development. In addition, our DPS team offers best-in-class analytical and specialized services for routine processes and troubleshooting in pharmaceutical manufacturing.
Discover More
For further information about our mammalian cell-culture capabilities for large-molecule drug substance, as well as for descriptions of Lonza’s mammalian cell culture facilities, please visit our mammalian manufacturing webpage. For further information about our microbial fermentation capabilities, please visit our microbial manufacturing webpage. For more information about our bioconjugate services, please visit our antibody drug conjugates webpage.
Our Global Footprint
Today our mammalian manufacturing offerings have a global footprint, and the company’s strength is providing the best option for our customers whatever their manufacturing strategy or stage of development.
We have the capability to produce clinical and commercial material across our sites globally, from small-scale (1,000–2,000L) through mid-scale (6,000L) to large-scale (10,000L and 20,000L).Lonza leverages its expertise in stainless steel, single-use and hybrid technology to de-risk the path to market for customers. We produce mammalian-derived biopharmaceuticals in highly advanced current good manufacturing practices (cGMP) multi-product facilities, in a global network across three continents: Slough (UK), Portsmouth, NH (USA), Tuas (SG), Porriño (ES), Visp (CH) and Hayward, CA (USA).
Our Slough (UK) site is the center of excellence for preclinical to clinical development and manufacture of mammalian-derived biotherapeutics. Our Portsmouth, NH (US) facility has been designed specifically for the production of therapeutic proteins derived from mammalian cell culture. In 2020, a new 6,000L mammalian suite, designed to manufacture next-generation molecules, is expected to be operational in Portsmouth. Our facility in Tuas, (SG) offers the full breadth of mammalian development and manufacturing services, from DNA to commercial cGMP products. In Porriño (ES), we specialize in the custom manufacture of recombinant proteins mammalian-derived. In Visp (CH), we offer our innovative IbexTM Solutions offering for biologics product lifecycle management for mammalian-derived biologics, microbial as well as bioconjugates. Our microbial center of excellence in Visp offers drug substance manufacturing solutions at capacities up to 15,000L and biosafety level 2 capabilities at all scales. Additionally, our bioconjugate team in Visp is one of the industry leaders in process development and cGMP manufacturing of clinical and commercial bioconjugates, including antibody drug conjugates (ADCs).
The newest addition to our mammalian manufacturing network is in Hayward, CA (US) — a site focused on clinical production of mammalian derived therapeutic proteins.
In China, as the country opens up to multinational companies, we are bringing our expertise in clinical development services and manufacturing. In 2020, a new mammalian site will be operational in Guangzhou (CN). The Guangzhou site will provide development and manufacturing services for early to late clinical and commercial launch projects. The new site will house a 17,000m2 multiproduct facility using single-use technology, with significant adjacent expansion land secured.
In Switzerland, we have acquired our first sterile drug product fill and finish facility. The facility in Stein (CH), complements our Pharma Biotech & Nutrition current parenteral drug product services in Basel (CH) and is the first facility for clinical production and commercial launches. It will enable us to build on existing parenteral drug product development and testing capabilities, and offer an end-to-end service to our customers for clinical supply and launch.
Highlights and Initiatives 2019
During the reporting year, we saw ongoing strong momentum for our clinical and commercial offerings in 2019. Commercial agreements signed for new and existing assets provide meaningful sales visibility for the mid- and long-term. Commercial capacities for 2020 are largely committed.
Our integrated clinical service offerings gained traction, with shortened development and manufacturing timelines, guaranteed delivery of drug product for IND (Investigational New Drug) applications and secured supply for subsequent clinical and commercial requirements.
Protein Expression
In 2019, we announced the next stage in the evolution of our GS Xceed® Toolbox. As the formats of innovative therapeutic proteins become more complex and harder to express, we are looking for new solutions to improve productivity for our customers. The launch of GS piggyBacTM technology enables the insertion of large DNA cargos into transcriptionally active and genetically stable areas of the genome. It allows the generation of stable pools of cells with high levels of protein expression. A further partnership with Synpromics to develop inducible promotors capable of turning gene expression “on or off” in response to signals in the cell environment, should enable fine-tuning of bioproduction. Both technologies are designed to provide even higher yields and enhanced performance and to support the expression of a growing number of challenging proteins including bi-specific antibodies and other new molecular formats.
Clinical Development and Manufacturing
We are committed to supporting a new generation of merging and even virtual Biotech companies looking to take innovative therapies into the clinic and beyond. An example of this is the partnership announced between Citryll and Lonza to manufacture NETosis Inhibiting Antibody CIT-013. This drug candidate offers new treatment options for various human diseases including lupus, vasculitis, pulmonary fibrosis and organ damage due to sepsis. Scientific teams from the two companies have been working together to develop Citryll’s lead antibody candidate CIT-013. Lonza’s in silico immunogenicity assessment services were used to improve the quality and potency of the candidate. Using our GS Xceed® System, we will create a cell line for the product and manufacture cGMP drug substance at our Slough (UK) site. Drug Product for this compound will be carried out at our recently acquired facility in Stein (CH).
IbexTM Design and IbexTM Develop
First customers for our innovative full-service, single-site clinical offering IbexTM Design and IbexTM Develop in Visp (CH) are committed. This constitutes 100% of 2020 available clinical manufacturing capacity one year ahead of planned operations.
One example is the extension of our partnership with Genmab to cover preclinical and clinical development and manufacturing for a significant portion of Genmab’s pipeline in IbexTM Solutions. Our Ibex Design offering enables Genmab to take their candidates from gene to IND in 12 months and then move to reserved manufacturing capacity in Ibex Develop for clinical manufacturing and BLA submission when Genmab needs it. The agreement aims to provide Genmab with security of supply and to enable Genmab to move rapidly into clinical manufacturing with the flexibility needed to manage an extensive pipeline through the demands of clinical trials.
Commercial Drug Substance Manufacture
Following the recent U.S Food and Drug Administration (FDA) approval of the Prior Approval Supplement (PAS) for second-generation-process Andexxa®, Portola Pharmaceuticals, Inc. and Lonza announced the start of commercial supply of the recombinant coagulation factor from Lonza’s Porriño (ES) facility. The production at our 10,000L mammalian facility in Porriño will be supplemented by additional large-scale capacity in IbexTM Dedicate at our Visp (CH) site. The two sites will ensure the flexible supply of Andexxa® to patients.
Additionally, we have recently signed a new IbexTM Dedicate deal with a major multinational pharmaceutical company for the manufacturing of a commercial microbial-derived product.
To satisfy increasing global demand for biosimilars, we have signed a contract with Celltrion to manufacture Remsima drug substance in our commercial facility in Singapore that will cover market needs in Europe and North America. The partnership will provide cost-effective biologics for greater patient benefit worldwide.
Bioconjugates
To meet increasing clinical, launch and commercial market demand, we started an expansion of our bioconjugation facility in Visp (CH). Now supporting the majority of commercially approved ADCs, we see the need to further expand based on signed commitments from customers.
Many bioconjugates are on expedited programs and the existing expertise at the facility, combined with proximity to clinical and commercial manufacturing of antibody, linkers and payload, will reduce risk and increase speed on the path to market for our customers.
Parenteral Drug Product Services
Our Drug Product Services (DPS) continued to expand ahead of plan, responding to positive demand from customers. Since entering the field of Drug Product Services at the end of 2016, we have met considerable demand from the market and have already announced various expansions. In 2019, we acquired a sterile fill and finish cGMP facility from Novartis, and we are currently already expanding capacity. From 2020 we will expand development and testing labs into a larger building in Basel (CH) with an additional 8,000 m² and we plan to hire additional experts. In Visp (CH), the IbexTM Solutions DPS fill and finish cGMP facility is progressing well and planned to be operational from end 2021.